News center
Contact us
Dongguan Ji kerr automation Technology Co., LTD
Telephone:0769-83328418
Fax:0769-83328428
Email:[email protected]
Address:80 Luxi Road, Xixi Village, Liaobu Town, Dongguan City, Guangdong Province
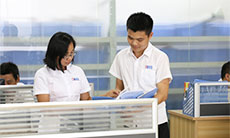
trade news
Home > News center > trade news
News center > trade news
How to use heat pipe in lithium battery thermal management system
Date:2022-03-05 browse:218
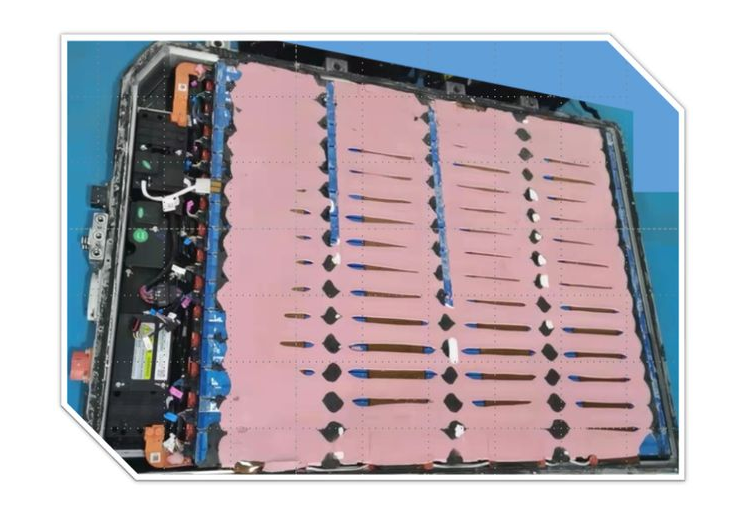
1 What is a heat pipe
Heat pipe, a highly efficient heat transfer device in a fully enclosed space, where capillary action drives liquid movement and temperature difference drives steam flow.
The cooling medium vaporizes in the high temperature region and condenses in the low temperature region.
The heat is transferred from the high temperature part to the low temperature part through the change of material state.
Microheat pipe
Micro heat pipe, as the name suggests, the size of the heat pipe is extremely small, the cross-section size is in the order of microns,
and the length is generally several centimeters. The working principle is similar to that of ordinary heat pipes, but there is no liquid suction core inside,
the channel section has sharp corners, and the condensed liquid mainly relies on the capillary action of sharp corners to return.
The micro heat pipe is mainly used in the extremely narrow range of integrated circuit boards, electronic chips, cpus and other Spaces, and the price is relatively high.
This paper mainly focuses on the thermal management of power battery packs, and the heat pipes mentioned later refer to ordinary heat pipes.
2 Working principle of heat pipe
The main components of the heat pipe: end cap, shell, fin (some do not), liquid suction core (capillary porous material), outer partition.
The left side of the partition is a low temperature environment, and the right side is a high temperature environment.
The coolant is heated and vaporized in a high temperature environment. Throughout the cavity, the left side is cold, the right side is hot.
Driven by differential pressure, steam flows from right to left in the chamber. After entering the low-temperature area,
it comes into contact with the low-temperature pipe wall and condenses into liquid state along the pipe wall.
The liquid coolant is adsorbed inside the material by the liquid suction material, subjected to capillary action,
and flows to the high temperature area without liquid pressure. The liquid returns to the high temperature zone and begins a new round of gasification cycle.
The outer fin of the heat pipe increases the contact area between the heat pipe and the heat transfer object, and improves the heat transfer efficiency of the heat pipe.
The separator separates the high temperature environment from the low temperature environment,
so that one section of the heat pipe can be in a high temperature environment and the other end is in a low temperature environment to obtain basic working conditions.
Heat pipe circulation phase change, heat transfer medium coolant, need to be a boiling point and application environment requirements match the liquid,
high temperature heat pipe need to add a high boiling point medium, at low temperature to maintain liquid;
Low temperature heat pipes require a medium with a low boiling point and a material that can be vaporized at a lower temperature.
The negative pressure environment inside the heat pipe is maintained, on the one hand, the boiling point of the coolant is reduced,
so that the material with high gasification temperature under normal pressure can also be used in the heat pipe;
On the other hand, the coolant gasification will increase the internal pressure of the heat pipe, artificially create the initial negative pressure conditions,
and offset a part of the negative pressure after the liquid gasification,
so as to avoid excessive pressure on the heat pipe shell caused by too much gasification of the coolant too fast.
From the working process of the heat pipe, it can be seen that the power of the flow of the gaseous medium comes from
the pressure difference brought by the liquid gasification between the high and low temperature regions. The liquid cooling medium,
the power to produce flow, comes from the capillary action of the liquid absorbing material.
capillarity
The explanation of capillary action is that "capillary action refers to the phenomenon of the infiltrated liquid rising in the fine tube and the phenomenon
of the non-infiltrated liquid decreasing in the fine tube" Capillary action occurs between solid and liquid, and different quality of solid and liquid,
its interaction is different, it should be said to be opposite. For the tube, the "soaked" liquid, the tube will promote its flow away from the liquid pool;
For "non-wetting" liquids, thin tubes prevent them from flowing away from the liquid pool.
The determined liquid can rise in the capillary tube diameter and material, and the corresponding formula can be calculated,
which is proportional to the surface tension of the liquid and inversely proportional to the diameter of the capillary tube and the density of the liquid.
Whether a liquid and a solid material are infiltrated or not, the reasons are different.
The most commonly used interpretation is that the contact of a liquid with a solid will first form an adhesive layer on the surface of the solid.
The liquid molecules on the adhesive layer are subjected to both liquid and solid molecular forces.
If the force between solid molecules and liquid molecules is greater than the force between liquid and liquid molecules,
the density of liquid molecules inside the adhesive layer increases, the repulsive force between liquid molecules increases,
and the liquid generates the power of outward expansion, extending upward along the tube wall, resulting in the phenomenon of infiltration.
On the contrary, if the force between the liquid molecules is greater than the force between the solid and the liquid,
the density of the liquid attachment layer is lower than the density inside the liquid, and an inward shrinking force is formed inside the adhesion layer,
and the adhesion layer itself has a tendency to shrink, resulting in no infiltration.
The material between the heat pipe suction core and the coolant must belong to the infiltration relationship before it can be applied.
3 Application areas of heat pipes
In 1964, Grover et al. proposed the current concept of heat pipes. It was first used in the aerospace military industry for temperature equalization
of space equipment and heat dissipation of space electronic equipment. Since then, radiator manufacturers have applied heat pipes to civilian equipment.
At present, the main application of heat pipes in the field of solar heat collection, industrial system waste heat recovery,
high-power power electronic device cooling temperature, the chemical industry in many links may use heat pipe heat absorption, heating, temperature balancing.
4 Classification of Heat pipes
There are many kinds of classification methods of heat pipes, divided according to the applicable temperature, divided according to the liquid reflux power,
divided according to the property of the shell and coolant material, and divided according to the structure of the heat pipe, which are not listed here.
The following content is classified according to the structure of heat pipes, focusing on recording several widely used heat pipe forms.
According to the structure form, it can be divided into ordinary heat pipe, flat heat pipe, separate heat pipe, radial heat pipe,
heat pipe of gross pump loop, miniature heat pipe and so on.
Ordinary heat pipe
The structure of ordinary heat pipes is as shown in the principle above, and the cross section shapes are round, flat, rectangular, etc.
The base area of the circular and most cooled objects is relatively small, but the structural strength is better.
The flat and circular section of the heat pipe is easy to fit with the plane, and the application is more, and the real section is shown in the figure below.
Copper tube shell, the shell inside the irregular layer is a liquid suction core.
Flat plate heat pipe
The flat type heat pipe is a rectangular plate in shape and is composed of a plurality of heat pipe channels inside.
The material of flat tube shell is mainly copper and aluminum. In a typical molding process, a number of wires are placed between the upper and lower two metal plates.
The plate and wire are welded together to form a whole. The space reserved between the two wires and the two plates becomes a heat pipe structure.
Flat heat pipe is a hot topic in research and application because of its simple structure and easy to realize large area heat dissipation.
The important index parameters of flat heat pipe are the heat transfer power per unit area and the ratio of power to heat pipe mass.
How much coolant can be filled into the heat pipe to obtain the best cooling effect is also one of the key points of research.
Annular heat pipe
The basic form of the ring heat pipe is shown in the following figure, and its working principle is slightly different from that of ordinary heat pipes.
The annular heat pipe can be designed to have no height difference and no suction core,
and the circulation mainly depends on the pressure difference of the two gas-liquid joint surfaces.
The liquid in the evaporation section is converted into gas by the action of external heat, and the pressure in the evaporation section rises.
The pressure pushes the gas down the steam line towards the condensing section. Near the condensing section,
the gas condenses into a liquid, and the space pressure is reduced.
In the whole working state, the pressure of the condensing section is always slightly lower than that of the evaporation section,
and the gas moves from high pressure to low pressure, forming the power to promote the gas movement.
When the evaporation rate changes, the gas-liquid bonding surface will be adjusted, and the pressure dynamic balance of the whole system will be constantly sought.
Pulsating heat pipe
Pulsating heat pipe, as shown above. On the whole, the pulsating heat pipe is also divided into three areas, evaporation section, adiabatic section and condensing section.
The diameter of the pulsating heat pipe is relatively small. After vacuum-pumping in the pipe,
part of the space is filled with liquid to form an spaced gas plug and a liquid plug, and the two are randomly distributed. In the evaporation section,
the liquid medium is thermally vaporized to form a bubble, and the pressure in the bubble increases to push the gas plug and liquid plug to the condensing section.
After reaching the condensing section, the gas liquefies and the gas plug shrinks or bursts. In this way,
the gas plug and liquid plug oscillate between the evaporation and condensing section, transferring heat. The basic principle is similar to the annular tube,
but the diameter of the tube is relatively small, and the capillary effect of the tube shell on the liquid is directly formed.
5 Application cases of heat pipes in thermal management of lithium batteries
In his paper "Design and Experimental Verification of Thermal Management System of Lithium battery Box based on Heat pipe Technology",
Zhou Haikuo designed and verified the application of heat pipe cooling in power lithium battery packs.
The authors chose the electrochemical-thermal coupling model of lithium battery to calculate the heat generation rate.
The equivalent thermal conductivity and equivalent specific heat capacity were estimated by taking the weighted average value of various materials,
and then the maximum heat generation rate and heat generation of the system were calculated.
Choice of cooling scheme. The intermediate interval of the battery pack is arranged with aluminum plate, which is fitted with the electric core to prevent,
as a heat collection device; The evaporation section of the heat pipe is embedded in the aluminum plate,
and the condensing section is assembled with the finned fan. As shown in the two pictures below.
For the integration of heat pipe and collector plate, the heat pipe is first embedded in the collector plate through the buried tube process,
and then welded by tin reflow to ensure full contact. The connection between the heat pipe and the fin is also processed,
and attention is paid to maintaining the maximum area of contact to reduce unnecessary thermal resistance.
According to the total calorific value and heating rate of the battery, select the type of heat pipe, diameter of heat pipe, material of heat pipe shell,
cooling medium model, liquid filling amount of heat pipe, fan power and fin shape.
The cooling object is a module composed of lithium iron phosphate soft pack cell.
The flow path of heat is: the battery generates heat, and through the aluminum plate,
the heat is comprehensively collected and transferred to the heat pipe embedded in the aluminum plate;
The heat pipe carries the heat to the condensing section through evaporation,
and then the fans and fins near the condensing section dissipate the heat into the surrounding space.
Comparison of simulation results of different cooling schemes
Aiming at the needling thermal runaway situation, the study compared the heat dissipation by fan only and the heat dissipation by fan heating tube through simulation,
and the ambient temperature was 20℃. The maximum temperature of the former system was 46.8℃ and the maximum temperature difference was 10.1℃.
The maximum temperature of the latter is 28.7℃, and the maximum temperature difference is 0.9℃.
The paper concludes that the heat pipe and fan cooling system can not only reduce the temperature difference of the system,
but also effectively reduce the adverse effects caused by thermal runaway in the case of abuse.
For the application of heat pipes in the lithium battery thermal management system, the main role is to transfer heat quickly from the high temperature system,
but the corresponding heat dissipation measures must be used together to provide good condensation conditions for the heat pipe,
in order to normally play the role of the heat pipe. Therefore, heat pipes can be used as auxiliary efficiency enhancement measures
for traditional thermal management systems such as air cooling and water cooling.